Coloring Enamel on Pocket Watch Dials
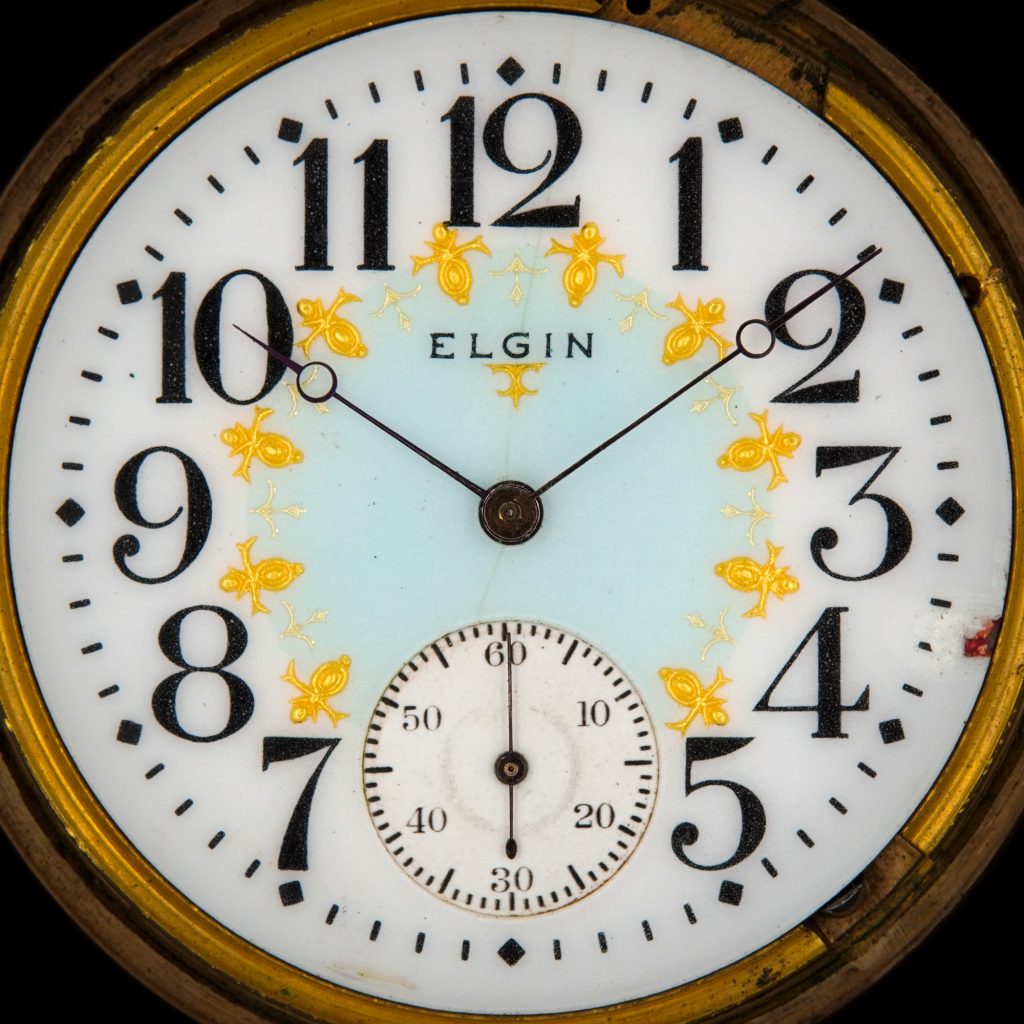
The 1880s proved to be a pivotal decade for the manufacturing of watch dials. Experimentation with different methods led to innovative techniques that ultimately changed the way dials were made.
Not only were new transfer techniques implemented to make the production more efficient but stunningly colorful enamel dials were introduced to the broad watch market.
The coloring process required a deep knowledge of chemistry, with each pigment resulting from a particular chemical reaction. The February 1883 issue of the Jewelers’ Circular and Horological Review provides insight into the components of various color mixtures:
White: Oxide of Tin
Yellow: Antimony Oxide, Antimorious Potash, Antimoniate of Potash, Antimoniate of Lead, Silver Oxide, Iron Oxide, Uranium Oxide
Red: Ferro-Oxide of Alumina, Sodio-Auric Chloride, Stannoauric Chloride, Cassius Purple
Orange: Mixtures of Yellow and Red-Brown Coloring Pigments
Green – Copper Oxide, Chromic Oxide, Protoxide of Iron
Blue: Protoxide of Cobalt, Silicate of Cobalt, Safflower
Violet: Manganese Oxide
Brown – Iron Oxide
Black – Protoxide of Iron in Larger Quantities
These colors were mixed into a stiff enameling paste with lavender oil and applied to the dial in accordance to the desired design. Because the fused enamel shrinks in volume when heated, the dial was often baked several times, adding another layer of enamel with each pass.
The elegantly colored enamel became a popular option for ladies’ watches, especially when combined with small gold or jeweled embellishments. Many gentlemens’ watches were also fitted with these “fancy dials,” offering a perfect watch to compliment social dress attire.
2 Comments