Manufacturing Process of the Sunk Seconds Bit on Early Enamel Watch Dials
The first dials manufactured by early American watch companies were flat. Not only was this form easier to produce, but it was necessary due to the enamel recipes being too reactive to the acid required to provision the sunk seconds bit.
In 1854, Aaron Dennison began experimenting to find a mixture that would allow acid to dissolve the copper without ruining the baked enamel. Around 1857, with the assistance of John Webb, a formula was found to produce sunk second dials. This formula was an intensely-guarded trade secret for several years while the process was perfected.
To achieve the sunk seconds bit, white enamel was first baked onto a copper blank before a special tool carefully bore a hole in the enamel down to the substrate. An acid was then used to dissolve the copper in the bare area, leaving a hole through the dial where a thin seconds bit was soldered to the dial. This created a sunken level for the seconds hand to rotate.
The accompanying photo exhibits the seconds bit on a c.1858 Appleton, Tracy & Co. dial, representing one of the earliest dials produced by an American company with a sunk seconds bit.
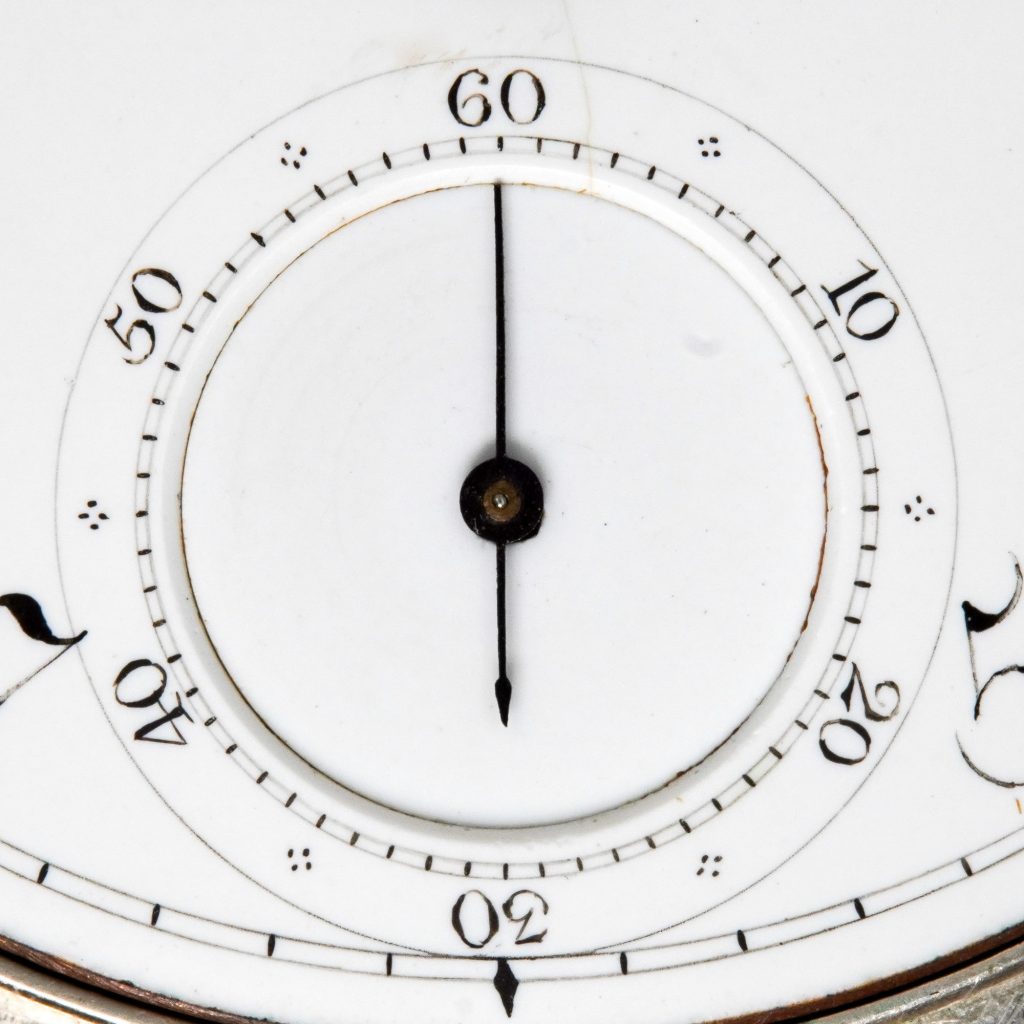
Great article! I wonder what the tool used too remove the enamel down to the plate looked like.
Excellent question. The descriptions I have read describe it as a thin copper strip that is shaped into a circle the size of the desired hole. As this is rotated at high speed, the sharp edge cuts into the enamel slowly until it stops at the copper substrate. It is not clear how long this method was used at the factory.
What is the new techinique now apart from welding it from the back
I am not really sure what you are asking. Please clarify. Thanks!