Venetian Hard Enamel vs. English Soft Enamel Dials: Part 1
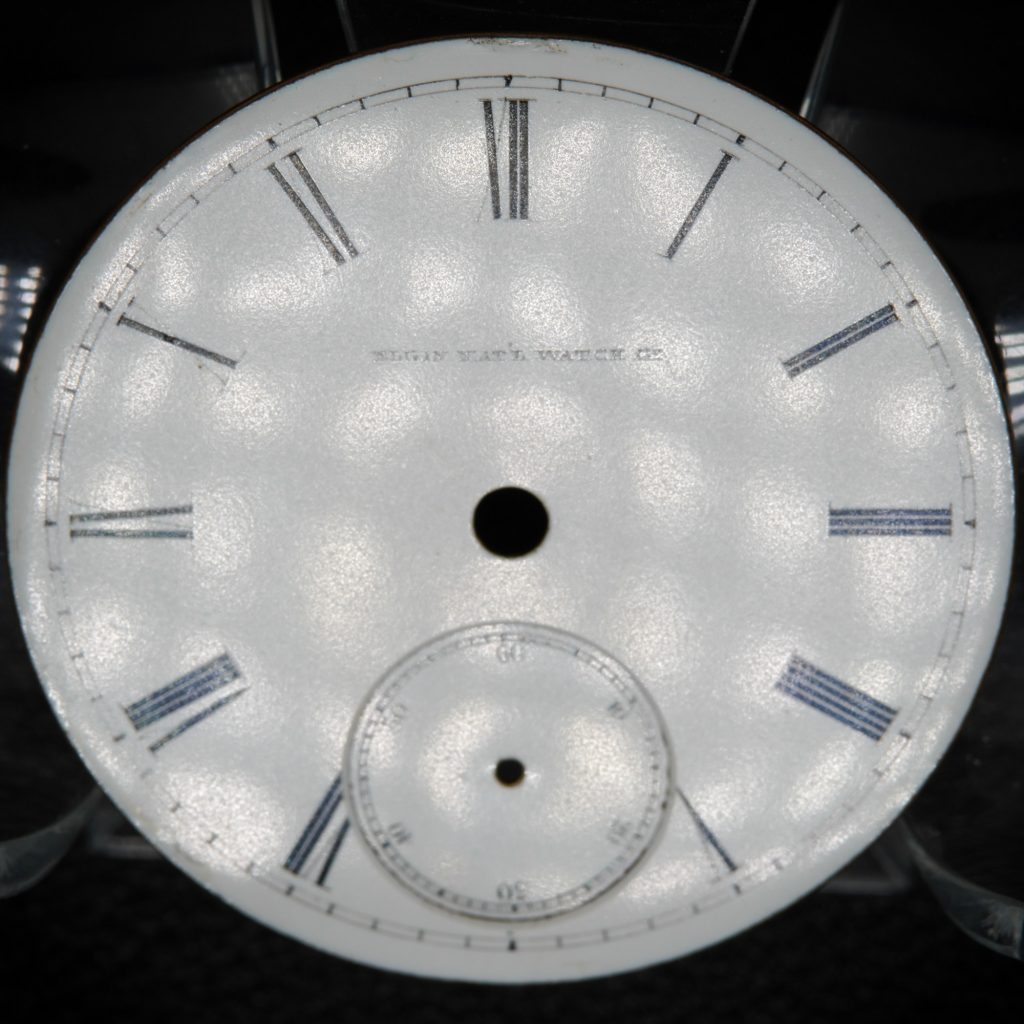
When the early American watch industry was sparked in the 1850s, the process of making enamel dials proved to be a challenge. Early attempts were unsuccessful, and in 1853, Aaron Dennison and Edward Howard sent John T. Gold to Europe to learn the process of making enamel dials.
When Gold returned with a powdered enamel recipe, the young company was finally able to make enamel dials and launch the American watchmaking industry.
These dials were made from Venetian enamel, commonly known as “Hard Enamel” in the trade. It was not until the early 1880s that “Soft Enamel” dials were introduced to the broad watch market in America.
The April 1900 issue of The Keystone described the process of preparing hard enamel:
“One of the great secrets of enameling lies in preparing the enamel. The enamel is not ground find, that is, to dust, but to grains about the size of very fine sand – No. 70 emery is about the proper size. The enamel is ground in an agate mortar, giving the pestle a sort of combined rocking and rolling motion with a certain pressure on the pestle. This certain pressure is only come at by practice and experience. All the very fine particles produced by the operation of grinding are washed away by adding water and pouring it off, the water carrying away all the very fine particles. The fusibility of enamels can be increased by adding glass of borax, which is simply borax heated red-hot and fused to a transparent glass. The use of this substance must be indulged in with extreme care, as it makes the enamel very soft, and even the acid used as a pickle will attack it. The ground enamel is made into a paste with water and filled into the recesses cut into the metal for its reception. Any person who has an enamel furnace can, by practice and perseverance, master the art enough to do a very credible job. The engraved recesses should be filled to excess so that the enamel can be ground off flat and smooth, and finally polished with tripoli and water.”April 1900 issue of The Keystone
As a result of this process, a hard enamel dial exhibits a slightly matte surface, enough to moderately diffuse light reflections as shown in the accompanying photo. This characteristic can be used to identify hard enamel by holding the dial at an angle sufficient to reflect direct light.
1 Comments